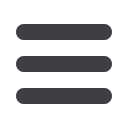
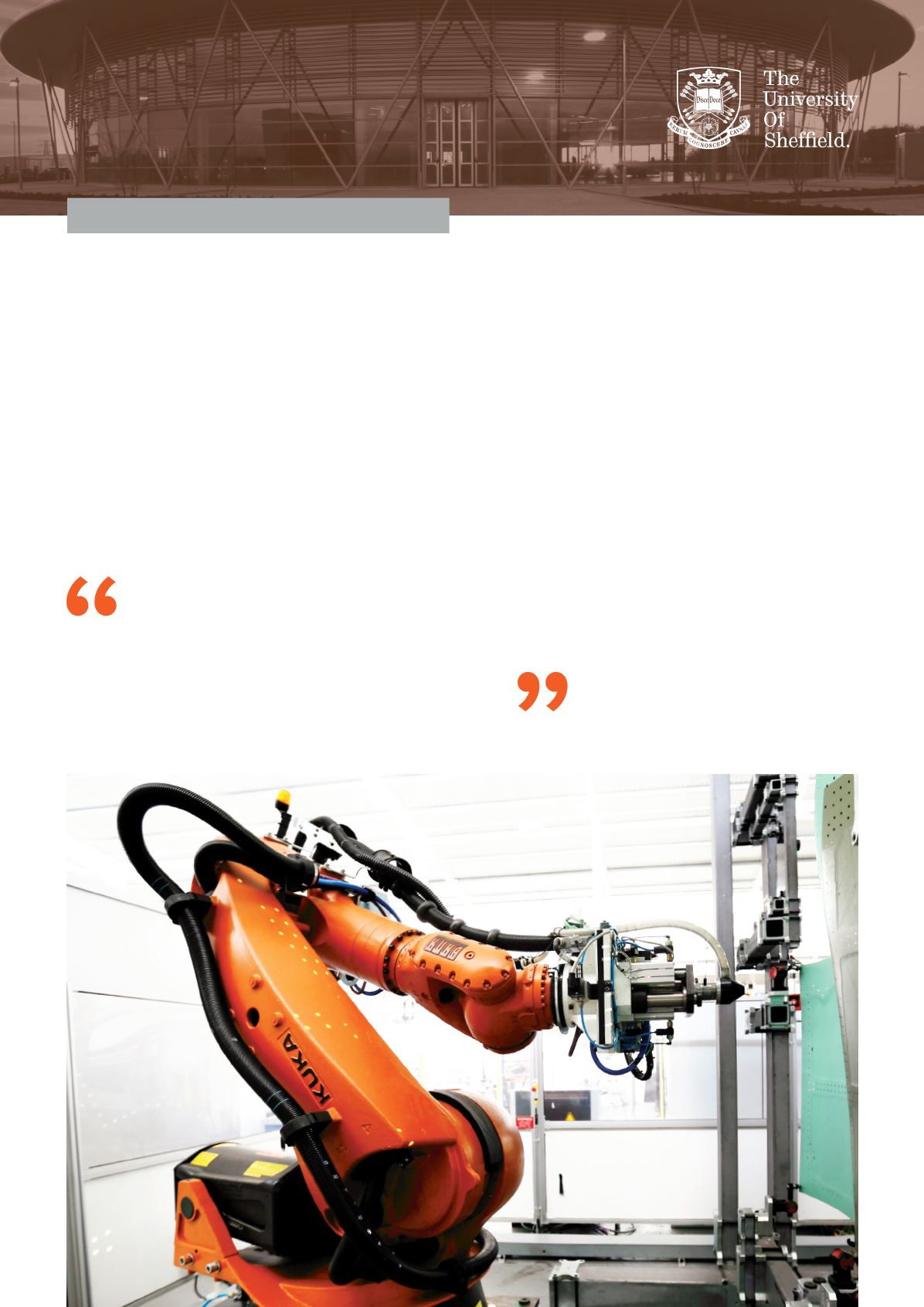
A research project to enable robots to
accurately machine holes in composite aircraft
components, has matured into a production
system which is on track to save BAE Systems
millions of pounds in capital and operational
costs over the coming years.
The Robotic Countersinking technology was developed through
collaborative research, led by the University of Sheffield’s
Advanced Manufacturing Research Centre (AMRC) and
involving Kuka Systems UK. The production system has now
been installed at BAE Systems in the UK, where it will be used
to process composite components for aircraft.
The Robotic Countersinking technology involves the use of
multiple robots to automatically handle composite components
and then countersink predrilled fastener holes. The system
includes the use of Augmented Reality to aid component
fixturing.
Austin Cook, from BAE Systems, said: “Since we began working
with the AMRC in 2006 it has supported the development of
key manufacturing technologies ranging from high performance
titanium machining to advanced automation for components.
The AMRC has helped us mature the Robotic Countersinking
technology from technology concept to full scale production
demonstrator, derisking along the way, and helping to catapult
the capability into our business.”
The AMRC has helped us mature the Robotic
Countersinking technology from technology concept
to full scale production demonstrator
Cutting the cost of producing
aircraft components
Case Study: Industrial Innovation
20